zui 誤區(qū)一:采用膠印軟片作為終輸出軟片
Zui myth 1: using offset film as the final output film
膠印軟片有著采購方便、經(jīng)濟(jì)、供貨及時(shí)等一系列優(yōu)點(diǎn),且工藝條件也相對(duì)成熟。但是,膠印軟片有一個(gè)致命的弱點(diǎn):表面過于光潔。感光樹脂柔性版在光聚合反應(yīng)過程中會(huì)釋放出一定數(shù)量的氧氣,只有磨砂軟片可以將這些氧氣順利地引導(dǎo)出去,使得軟片與版材仍保持等應(yīng)接觸,精確地轉(zhuǎn)移影像。
Offset film has a series of advantages such as convenient procurement, economy and timely supply, and the process conditions are relatively mature. However, offset film has a fatal weakness: the surface is too smooth. The photosensitive resin flexographic plate will release a certain amount of oxygen during the photopolymerization reaction. Only the frosted film can guide these oxygen smoothly, so that the film and the plate still maintain equal contact and accurately transfer the image.
與此相反,膠印軟片表面光潔,不能將氧氣順利地導(dǎo)出,導(dǎo)致軟片與版材之間的間隔變大,引起圖像變形、圖文變粗、模糊等故障。有些制版操作人員采用撒爽身粉的辦法,一定程度上緩解了這些問題,但是同時(shí)也導(dǎo)致透光率下降,增加了片的云霧度。
On the contrary, the surface of offset film is smooth and smooth, and oxygen can not be exported smoothly, resulting in larger spacing between film and plate, resulting in image deformation, coarsening and blurring. Some plate making operators use the method of sprinkling talcum powder to alleviate these problems to a certain extent, but at the same time, it also leads to the decrease of light transmittance and the increase of cloud haze of negative film.
誤區(qū)二:印前系統(tǒng)配置不合理
Myth 2: unreasonable prepress system configuration
由于柔印的專用軟件比較昂貴,非一般中小型制版公司可以承受,所以目前國內(nèi)只有少數(shù)幾家海外公司消費(fèi)得起,而絕大多數(shù)制版廠商則進(jìn)行了因地制宜的國產(chǎn)化。一般而言,小規(guī)模的制版廠大多采用平臺(tái)掃描儀和數(shù)字相機(jī)作為輸入設(shè)備,修正電腦采用的PC或蘋果G3,再加上照排機(jī)、沖片機(jī)作為輸出裝備。
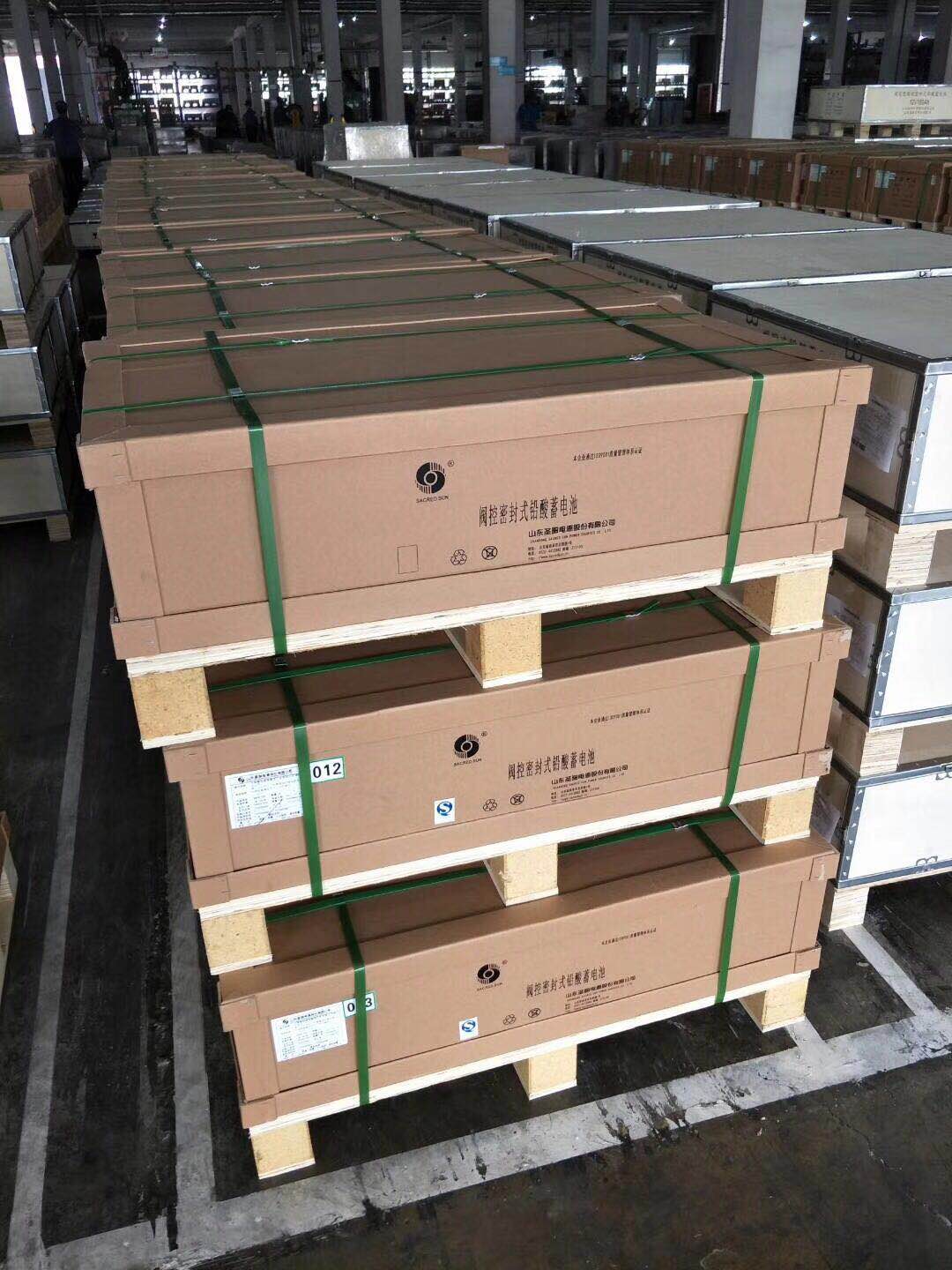
As the special software for flexographic printing is relatively expensive and can not be borne by ordinary small and medium-sized plate making companies, at present, only a few overseas companies in China can afford it, while the vast majority of plate making manufacturers have made localization according to local conditions. Generally speaking, most small-scale plate making factories use platform scanners and digital cameras as input equipment, modify the PC or apple G3 used by computers, and add phototypesetters and film processors as output equipment.
由于受制版規(guī)模的限制,所以許多國內(nèi)廠家照搬膠印制版的配置,甚采用打印輸出加照相等滯后技術(shù),使得國內(nèi)的瓦楞紙箱柔印技術(shù)一直處于一種水平的狀態(tài),僅僅作為手刻橡膠版的替代品,尚未進(jìn)入彩色瓦楞紙箱印刷的時(shí)代,與國外同行相比,我們落后了將近10-15年。
Due to the limitation of plate scale, many domestic manufacturers copy the configuration of offset plate making, and even adopt lag technologies such as print output and photography, so that the domestic corrugated box flexographic printing technology has been at a low level. As a substitute for hand carved rubber plate, it has not entered the era of color corrugated box printing. Compared with its foreign counterparts, We are nearly 10-15 years behind.
誤區(qū)三:版材的選型比較盲目
Myth 3: plate selection is blind
許多制版企業(yè)沒有考慮印刷廠的實(shí)際情況,如印刷機(jī)的型號(hào)、貼版膠帶的厚度、使用油墨的類型等,盲目地從眾。以瓦楞紙箱用的印版為例,許多客戶僅僅知道杜邦公司非常著名的TDR型版材。
Many plate making enterprises blindly follow the crowd without considering the actual situation of the printing factory, such as the model of the printing press, the thickness of the plate pasting tape, the type of ink used, etc. Taking the printing plate for corrugated box as an example, many customers only know the famous TDR plate of DuPont.
TDR是一種廣泛使用的瓦楞紙印刷版材,具有優(yōu)異的制版性能,但分辨力不如EXL/UXL等一批薄版來得高。在印刷E型瓦楞以及高達(dá)120線/英寸的圖像時(shí),應(yīng)換用EXL/UXL等薄版,并加以海綿襯墊,這樣才可獲得高分辨力。同時(shí),隨著版材硬度的提高,還可減少網(wǎng)點(diǎn)擴(kuò)大,使印品達(dá)到的效果
TDR is a widely used corrugated printing plate with excellent plate making performance, but its resolution is not as high as a batch of thin plates such as EXL / UXL. When printing E-type corrugated and images up to 120 lines / inch, thin plates such as EXL / UXL should be replaced with sponge pads to obtain high resolution. At the same time, with the improvement of plate hardness, it can also reduce the dot expansion and achieve excellent printing effect